Besøg hos produktionsvirksomhed med montagelinje Helmut og jeg besøgte i sidste uge en produktionsvirksomhed. De…
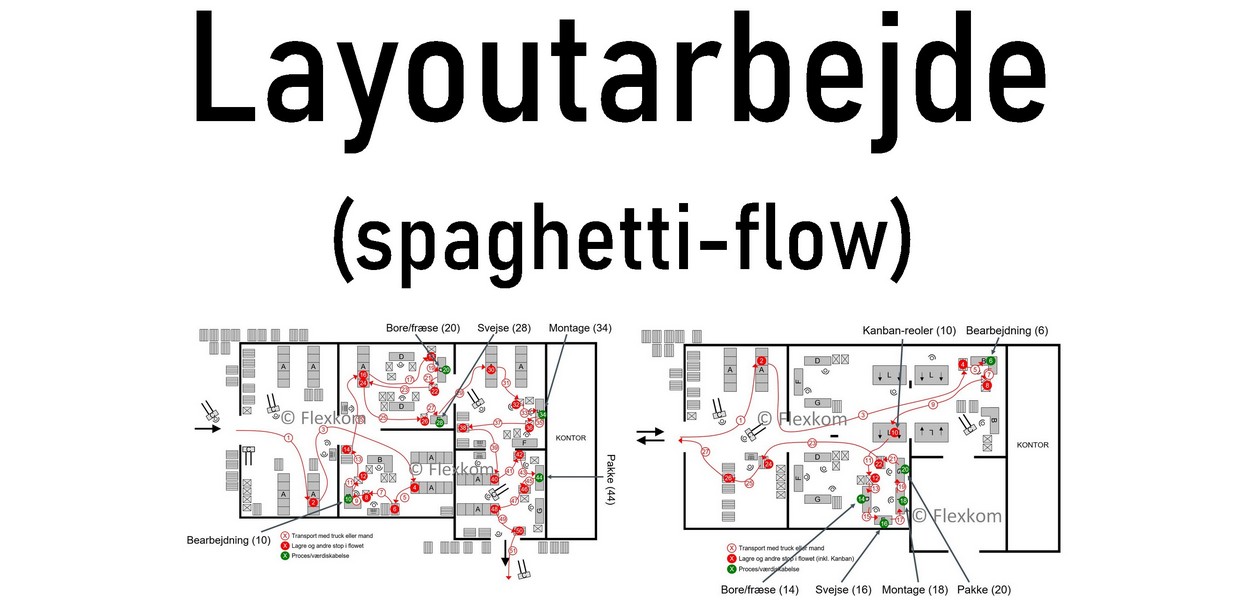
Senest opdateret 4. januar 2024
Layoutoptimering og spaghettidiagram i en produktion
Vi vil lige dele lidt eksempler og erfaringer med layoutoptimering og spaghettidiagrammer.
#1: Værdistrømsanalyse
Det er altid klogt at danne sig et overblik. Her er værdistrømsanalyse et uundværligt værktøj (i vores verden :-)).
Her får man et unikt overblik over processer, procestidertider, omstillingstider, oppetider osv.
Typisk laver man først en current state og derefter en future state. Imellem de to ligger en handlingsplan og målsætninger. Og efter future state ligger selve implementeringen.
- Se en video om værdistrømsanalyse i en produktion >
- Læs mere om VSA/VSM Værdistrømsanalyse >
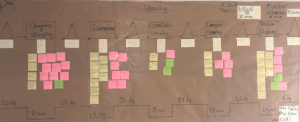
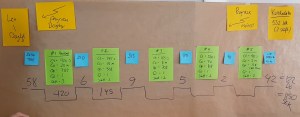
#2: Tidsoverblik – “Yamazumi” og “Manufacturing Critical Path Time”
For at få et overblik over tider, tidsafhængigheder, tidsrøvere m.v. så anvender vi Yamazumi og MCT-tidstrappe.
Dansk Lean Forum:
Certificeret Lean Green eller Black Belt?
Alle bælteniveauer – som selvstudie eller fremmøde >
Yamazumi er det grundlæggende værktøj i flow-forståelse – her jagter vi udjævning af flaskehalse.
Læs mere om Yamazumi – tidsudjævning og flow >
En udfordring ved Yamazumi er, at mange i dag har en såkaldt “variantfabrik”. I en variantfabrik varierer flaskehalse, flow/ruter og tider nærmest fra time til time. Derfor skal udjævning foregå meget dynamisk – eks. via daglige Daily Huddle planlægnings-tavlemøder >
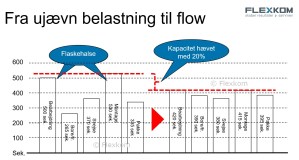
For at få et overblik over gennemløbstiden og de store “tidsrøvere” er MCT-tidstrappen et fantastisk værktøj. Det er hentet fra QRM (Quick Response Manufacturing).
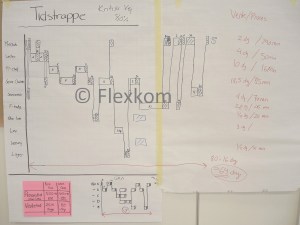
#3: Spaghettidiagram
Derefter kommer et arbejde med at evaluere og måske forbedre det fysiske layout.
Dansk Lean Forum:
Fuld effekt af Lean?
Målstyring, fra hamster- til forbedringshjul, stærk problemløsning…
Vi har hjulpet Toyota – mød Flexkom >
Processen starter ofte med spaghettidiagrammer. Her får man et overblik over medarbejdernes og varernes ruter under en ordre.

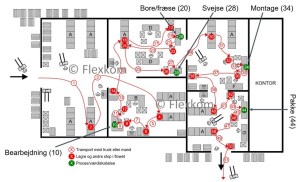
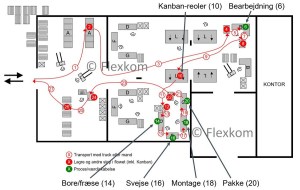
#4: Inputs til layout
Et godt princip er, at vi søger mod u-celler. Men kun hvor processerne er egnet til det! Det kræver, at varerne/varefamilien skal igennem cirka de samme processer, at processerne er tidsmæssigt udjævnet, at processerne er stabile i procestider og omstillingstider m.v. Ellers er celler uden ret meget mellemvarelager farlige!
Jeg har set en produktion, som engang ændrede en større montageafdeling til en u-celle. Men processerne var ustabile og ikke i takt. Det hele brød sammen! Og det tog MEGET lang tid før de var tilbage med samme kapacitet!

Overvej også inspiration i Bucket Brigade udjævningsprincippet ved celler og montagelinjer. Læs mere via link.

#5: Fysisk layout
Nu skal vi så designe det fysiske layout. Det bedste værktøj er nok LEGO. Fordelen ved at bygge layoutet er, at man får det i 3D. Så man kan fornemme om den høje reol bliver et problem osv! Men det er lidt omfattende med LEGO.
Alternativt klip en masse modeller af borde, reoler, maskiner osv. I det samme målestoksforhold. Og lav et layout på pap – som alle kan kigge på. Det er en stærk metode til debatter og involvering.
HUSK: Jeg har én gang hjulpet med en fabriksflytning. Og her havde man droppet alt om affaldsstationer, papstationer, reoler osv. For man skulle jo være Lean i den nye fabrik – og i Lean er der ingen lager…og åbenbart heller ingen affald!
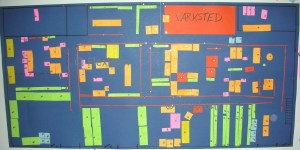

#6: Rentegning af layout
Rentegning er altid en god ide. Både for at sikre os, at pap-layoutet holder i virkeligheden. Og også for at kunne definere forsyning (husk at gøre det fleksibelt fra loftet – ikke i gulvet) osv.
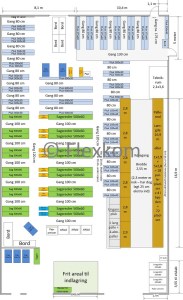
#7: Fysisk flytning
Og nu skal der så flyttes, etableres forsyning osv. Det er en fed proces :-)
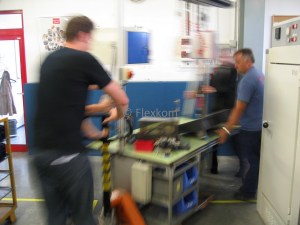
Læs mere
- Læs mere om “hvad er flow i en produktion” >
- Læs mere om Lean Produktion >
Dansk Lean Forum
Af Mikkel Smith, Flexkom
Dette indlæg har 0 kommentarer